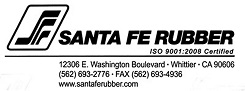
Design Tooling

Mold Types...
Typical methods used in the manufacture of rubber products include compression, transfer and injection molding. The tooling for each product varies depending on the process employed.
|
|
Compression Molds: Compression molds vary in size, shape, and complexity. A simple single cavity compression mold is shown in figure 1. An uncured rubber pre-form is placed in the cavity prior to mold closure. During closure, the rubber is squeezed between the top plate and the cavity plate with the excess flowing into the flash groove. The thickness of flash above the land and the volume of flash in the flash grove will vary. The variable thickness of flash between the top plate and the land causes closure dimensions to be less accurate than the dimensions fixed within the cavity.
|
Tolerances for fixed and closure dimensions must be determined accordingly. Dowel pins provide proper registration between mold plates and can be arranged in such a manner as to prevent improper mold assembly.
|
|
|
A small compression mold may have handles and a hinge in back which allow the mold to be removed from the press between heats. Large molds are usually attached to the press plates so they may open and close with the press. Santa Fe Rubber prefers this mounted method since it minimizes the amount of abuse the mold is subjected to during handling. Mounted molds also facilitate the use of slide trays and loaders and minimize heat dissipation, which can dramatically improve productivity.
|
Transfer Molds: In transfer molds, a plunger compresses a rubber pre-form in a pot as shown in figure 2. When the press closes on the mold, rubber flows through the sprue and into the mold cavity. Each cavity has at least one sprue. Being funnel shaped, the diameter of the sprue decreases as it approaches the cavity. Because the sprue narrows just above the molded part, the sprue breaks at this point, when the flash pad is removed from the transfer pot. Thus the major portion of the sprue remains affixed to the cured flash pad and is removed when the pot is cleaned.
|
|
|
Injection Molding: In injection molding, a strip of uncured compound is commonly fed into the injection machine, eliminating the pre-form associated with compression and transfer molding. Molds for this process are more complex since the compound is automatically metered into the cavity, cured and ejected. Injection molds typically have multiple plates and sprue cavities through a gate. Injection molds may also include various heat or vacuum zones, indexable cavity inserts and an injection system.
|
Mold Materials...
The cost of molds sometimes seems unjustifiable until you look at the hidden costs. A cheap mold made with relatively "soft" steel or aluminum may look good up front, but when a mold of this construction begins to wear prematurely, its hidden cost becomes quickly apparent. Soft steel and aluminum molds typically have a life of only a few thousand cycles (heats), while J-45, hardened steel or NAC may last up to a million or more. This longevity lowers costs due to mold wear, down time and re-work or replacement. Over the total life of a mold, these savings can justify the "up front" costs by a factor of two or three times.
|
|
We're Very Tolerant...
Today, demanding applications seem to involve ever tighter dimensional tolerances. The mechanical properties that make rubber so useful, the ability to rebound after deformation, also make it difficult to measure. Precision tolerance can be achieved in molded rubber products by employing elaborate tooling, manufacturing and finishing processes. However, overly complex processes due to mis-specified tolerances often result in unnecessary and prohibitive costs. Factors affecting tolerances in the design stage include part volume, material shrinkage after cure, reduced shrinkage from bonded inserts and fixed vs. closure dimensions. In order to maintain cost efficiency Santa Fe Rubber suggests these Standard Tolerances when designing finished products.
|
|